液液萃取作为一种重要的分离技术,广泛应用于化工、制药等领域。然而,乳化现象的存在往往成为这一技术的瓶颈,影响分离效率和产品质量。乳化不仅增加了操作难度,还可能导致设备堵塞、产物损失等问题。因此,如何有效解决乳化现象,成为行业关注的重点。以下从几个方面探讨液液萃取过程中乳化现象的解决策略。
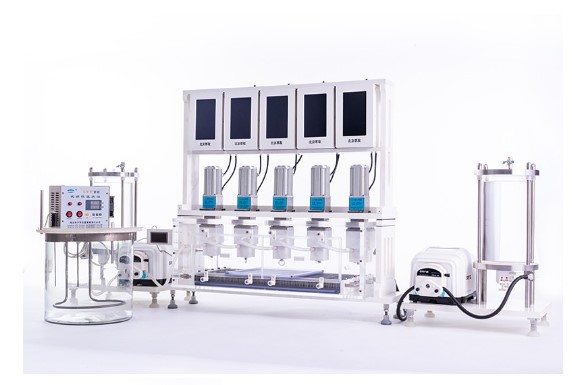
一、乳化现象的成因分析
乳化是指两种不相溶的液体在搅拌或传质过程中形成稳定乳状液的现象。其成因复杂,主要包括以下几点:
搅拌不当:搅拌速度过快或搅拌器设计不合理,容易导致液体剧烈混合,形成细小的液滴,增加乳化风险。
表面活性物质:溶剂或原料中含有的表面活性剂,能够稳定乳状液的界面张力,使其难以分离。
杂质影响:液体中的固体颗粒或不溶性物质可能吸附在液滴表面,进一步增强乳化稳定性。
液体性质差异:当两种液体的密度、黏度相近时,乳化现象更容易发生。
二、物理方法:直接打破乳化平衡
物理方法是解决乳化问题的常用手段,具有操作简便、环境友好的特点。
静置分离:对于轻度乳化的体系,可以通过静置让液滴自然上浮或下沉,从而分离。虽然耗时较长,但在某些场景下仍是有效选择。
离心分离:利用离心力加速液滴的分离,是一种高效的方法。离心萃取机在处理乳化问题时表现尤为突出,能够快速打破乳化平衡,提高分离效率。
改变搅拌方式:适当降低搅拌速度,或调整搅拌器的形状和位置,可以减少液体的剧烈混合,从而降低乳化发生的可能性。
三、化学方法:从根源消除乳化
化学方法是解决乳化问题的重要途径,主要通过添加试剂或调节溶液性质来实现。
破乳剂的使用:破乳剂能够破坏乳状液的稳定性,促使液滴聚合并分离。例如,某些有机溶剂或表面活性剂的反离子,能够有效降低界面张力,帮助乳状液分离。
调节pH值:溶液的酸碱性会影响表面活性物质的性质。通过调节pH值,可以改变乳化液的稳定性,从而减少乳化现象的发生。
去除杂质:通过过滤或沉淀等方式去除溶液中的固体颗粒和杂质,可以显著降低乳化风险。
四、设备优化:减少乳化发生
设备的合理设计对预防乳化现象具有重要意义。以下是一些常见的设备改进措施:
选择合适的萃取器:离心萃取机因其高效的分离能力和对乳化现象的低敏感性,成为解决乳化问题的理想设备。其高速旋转产生的离心力能够快速分离液滴,避免乳化现象的产生。
优化流道设计:在填料塔或板式塔中,合理的流道设计可以减少液体之间的剪切作用,降低乳化的发生概率。
液液萃取过程中的乳化现象虽然常见,但并非不可克服。通过物理方法打破乳化平衡、化学方法消除乳化诱因、设备优化减少乳化风险,行业从业者能够更好地应对这一挑战。同时,结合实际案例的研究与探索,为解决乳化问题提供了更加系统化的方案。乳化问题的解决不仅提高了液液萃取的效率和精度,也为化工、制药等行业的技术进步提供了重要支持。